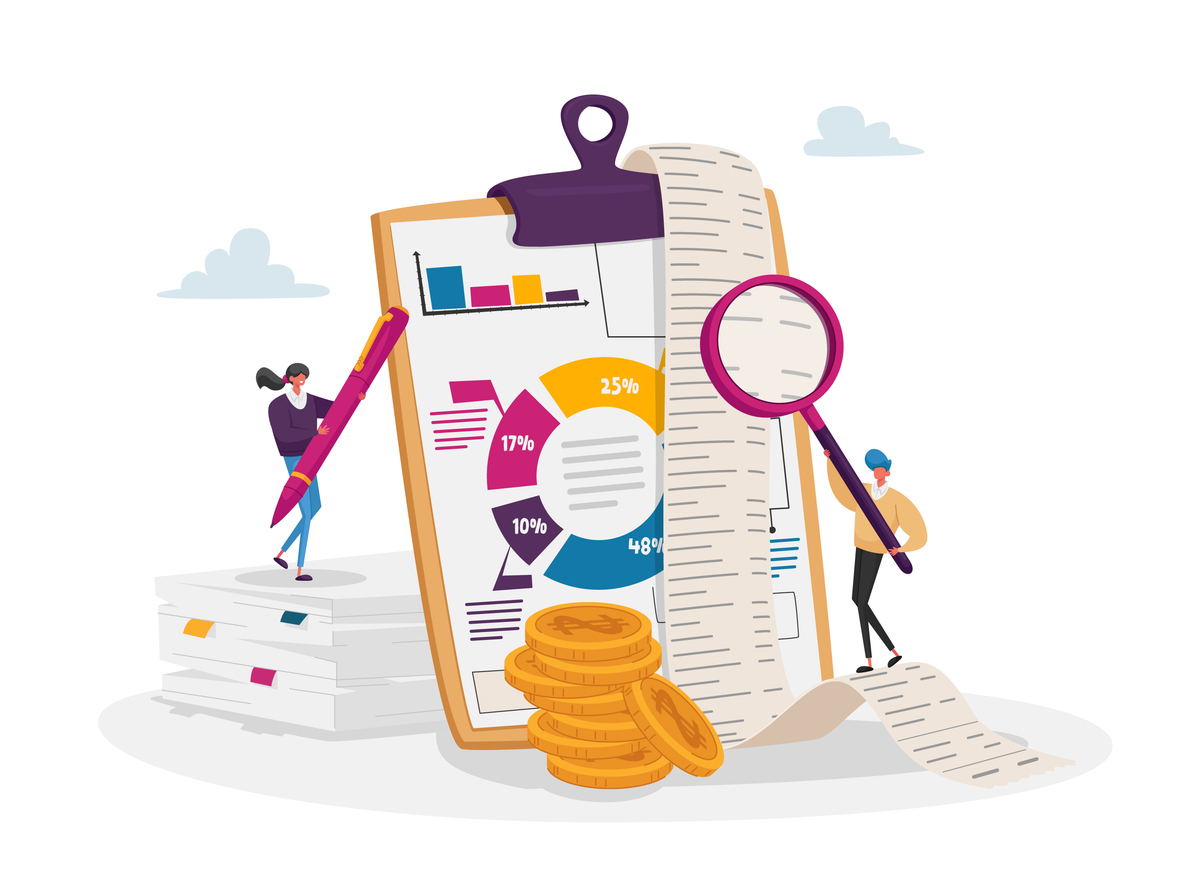
Introduction
As vehicles become more technologically advanced, ensuring accurate repairs and maintenance is crucial for safety and performance. Original Equipment Manufacturer (OEM) service information plays a pivotal role in achieving this goal. This article explores why using OEM service information is essential for body shops and repair facilities.
What is OEM Service Information?
OEM service information consists of detailed guidelines, procedures, and specifications provided by vehicle manufacturers. These documents cover everything from repair procedures and diagnostic steps to parts specifications and safety guidelines. They are designed to ensure that repairs are performed correctly, using approved methods and components.
Benefits of Using OEM Service Information
Using OEM service information offers several key benefits:
- Accuracy and Reliability: OEMs design their vehicles with specific parts and systems that work together seamlessly. Using OEM service information ensures that repairs and replacements maintain the vehicle's original integrity and performance standards.
- Compliance with Manufacturer Standards: Following OEM guidelines ensures that repairs meet the manufacturer's quality and safety standards. This compliance is essential for maintaining vehicle warranties and ensuring optimal vehicle performance.
- Access to Up-to-Date Information: OEMs continuously update their service information to reflect new technologies, safety recalls, and improved repair techniques. Accessing this updated information helps repair facilities stay current and informed.
- Support for Diagnostic and Repair Procedures: OEM service information provides detailed diagnostic procedures and troubleshooting steps. This support is invaluable for accurately identifying and resolving vehicle issues.
Ensuring Vehicle Safety and Performance
Vehicle safety relies heavily on proper repairs and maintenance. Using OEM service information ensures that safety-critical systems such as Advanced Driver Assistance Systems (ADAS), brakes, airbags, and electronic components are repaired and calibrated correctly. This approach enhances vehicle safety and reduces the risk of malfunctions or failures.
Challenges of Non-OEM Parts and Procedures
Deviation from OEM service information poses several risks:
- Compatibility Issues: Non-OEM parts may not fit or function correctly with the vehicle's existing systems, leading to performance issues or safety hazards.
- Voided Warranties: Using non-OEM parts or procedures can void vehicle warranties, leaving vehicle owners responsible for repair costs.
- Legal and Liability Concerns: In some cases, using non-OEM parts or procedures may result in legal liabilities if the vehicle fails to meet safety standards or causes accidents.
Best Practices for Using OEM Service Information
To maximize the benefits of OEM service information, consider the following best practices:
- Access Authorized Sources: Obtain OEM service information directly from authorized sources such as manufacturer websites or authorized dealership networks.
- Invest in Training: Ensure technicians are trained and certified in using OEM service information and following manufacturer guidelines.
- Stay Updated: Regularly check for updates and revisions to OEM service information to incorporate new procedures and recommendations.
- Document Procedures: Maintain detailed records of repairs and calibrations performed using OEM guidelines, including parts used and procedures followed.
Conclusion
Using OEM service information is essential for maintaining vehicle safety, reliability, and performance. It ensures that repairs are conducted to the highest standards, complying with manufacturer specifications and warranty requirements. By prioritizing OEM guidelines, repair shops and technicians can uphold customer trust, enhance vehicle longevity, and contribute to overall road safety.